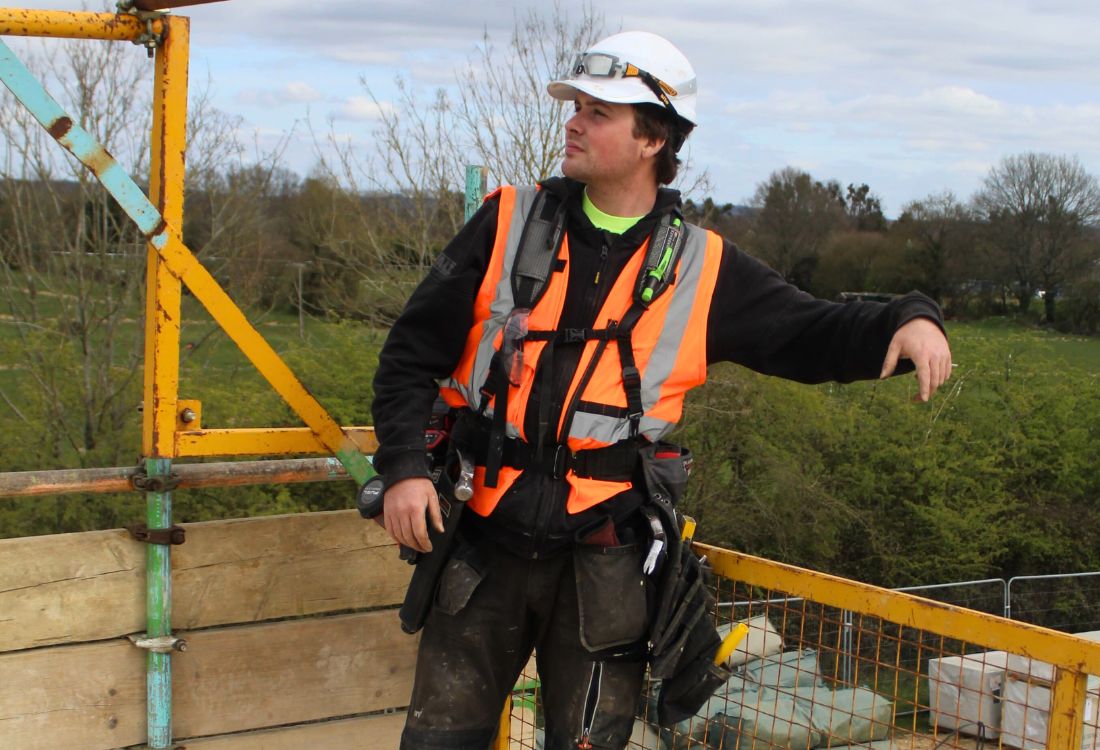
10 Crucial Health And Safety Regulations For Your Construction Site
Health and safety legislation is designed to encourage uniform safe working practices on construction sites throughout the country, and keep people safe at work. As a construction business owner or main contractor, it’s your responsibility to maintain a safe workplace in compliance with current health and safety regulations; it is also important to bear in mind that failing to comply with these regulations can lead to expensive fines, legal issues, and potential hazards to your workers.
Following these top regulations, and more as specified on the Gov.UK website, will keep your construction site legal, and ensure you know how to identify and reduce the risks of working in this dangerous industry.
1. The Construction (Design & Management) Regulations
This regulation is in place to ensure that health and safety are considered during the entire process of designing and constructing a building. It requires the appointment of a competent principal designer and principal contractor and sets out a shared responsibility for the safety of the site.
The regulations establish a legal framework for how to:
- Identify, manage and minimise risks on site.
- Consult and engage with workers about those risks.
- Identify the right people for the right job.
- Ensure the safety of you and your workforce.
2. Working at Height Regulations (2005)
Working at height is one of the most risky elements of the construction trade, and so the Working at Height Regulations were established to prevent falls from height – and thus avoid the most common cause of death and serious injury in construction work. The law requires employers to ensure that all work is planned, supervised and carried out in a way that prevents falls.
3. The Health & Safety (First Aid) Regulations
As an employer or site manager, you are required to provide suitable first aid equipment and facilities, as well as trained personnel, to ensure that any injuries or illnesses are treated promptly and appropriately. This can include providing first aid kits, trained first aiders, and even medical equipment like defibrillators.
4. The Lifting Operations and Lifting Equipment Regulations (LOLER) 1998
The LOLER regulations apply to the operation of any equipment used for lifting or lowering, such as cranes, hoists, and even hand-operated tools like jacks, ensuring that lifting operations are rigorously planned and that the appointed person, plant operator, lift supervisor, slinger/signallers and everyone else involved are trained, qualified, and competent to carry out their tasks safely and efficiently. As an employer, you will need to ensure that lifting equipment is properly maintained, inspected, and used by qualified personnel in a compliant manner.
5. Control of Asbestos Regulations 2012
Asbestos-related diseases are responsible for thousands of deaths each year in the UK. If your construction project involves working with asbestos-containing materials (ACMs), you will need to follow strict regulations aimed at protecting your workers and subcontractors from exposure. This could include identifying potentially hazardous materials, restricting access to the work area, or even bringing in specialist contractors to safely remove any asbestos.
6. Control of Vibration at Work Regulations 2005
If your workers are exposed to high levels of vibration, such as from using power tools or heavy machinery, they could be at risk of developing conditions like hand-arm vibration syndrome. These statutes require site managers and main contractors to assess the risks of vibration exposure and take steps to reduce or eliminate it where possible. The regulations provide information on the level of exposure which is legal, the transitional period between exposures, and the risks of overexposure.
7. Control of Noise at Work Regulations 2005
Exposure to high levels of noise can cause permanent hearing damage and other health problems to on-site operators, workers, and members of the public. Control of Noise regulations require employers to evaluate noise-associated risks and put mitigating measures in place, such as by using noise-reducing barriers or providing hearing protection to workers. Ultimately, these regulations aim to safeguard the hearing of workers, preventing hearing loss and/or development/progression to tinnitus from occurring. One rule within these regulations is for effective hearing protection to always be available and provided, as well as hearing protection zones to be implemented on every site.
8. Manual Handling Operations Regulations 1992
If your workers are responsible for lifting heavy loads or performing repetitive manual tasks, they could be at risk of developing musculoskeletal disorders like back pain. These regulations are mainly for yourself and safety representatives, but useful for anyone working on-site to know as they cover how to avoid, assess, and reduce the risk of injury from manual handling. Manual handling regulations require site managers to provide adequate lifting equipment or training in safe lifting techniques in order to mitigate risk and avoid unnecessary injuries.
9. The Electricity at Work Regulations
Electricity is a common hazard on construction sites, and improper use or maintenance of electrical equipment can lead to serious injuries or even death. The electricity at work regulations establish an electrical safety framework to minimise the risk of injury or death from electrical hazards, and what to do in the event of an emergency happening due to electrics.
10. The Gas Safety Regulations
If your construction project involves working with gas, such as the proximity of a gas mains outlet or plumbing during a housing development, you will need to follow strict regulations aimed at protecting your workers and the public from gas leaks or explosions. Adequate training, preparation, and equipment should be provided to people responsible for overseeing, managing, installing or handling gas appliances or fittings, to ensure no injury or emergency occurs.
What next?
Running a safe and healthy construction site requires a lot of work and attention to detail, but by following these ten crucial UK health and safety regulations, you can create a safer work environment for your employees and avoid costly fines and legal consequences for non-compliance.
Some of the steps SC4 takes to ensure health and safety on site include:
- SMAS SSIP Accreditation
- Detailed RAMS for all works
- Appointed Person (APs), Crane Supervisors and slingers/signallers to ensure any crane lifts, etc, are carried out safely.
- SMSTS (Site Management Safety Training Scheme) and SSSTS (Site Supervisor Safety Training Scheme) trained managers and supervisors
- Qualified workforce that holds up-to-date CSCS cards
- Regular PAT testing of electrical tools
- Compulsory PPE including face-fit testing of masks
- Regular Toolbox talks and communication on safe working methods
- Trained First Aiders and Mental Health First Aiders
Please get in touch today to find out more about our health and safety policy and how we help promote a safe and productive environment in all our construction projects.
Click on the categories below to find out more about:
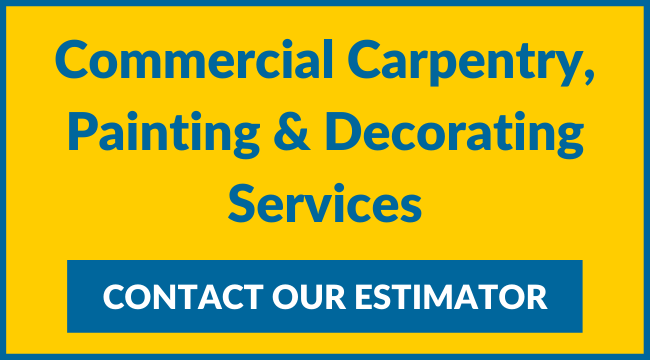
Connect with Us
Share this Page
More Posts
Recent Posts
- Our Favourite Carpentry Project Of 2024: Cromwell Court, Old Basing
- Case Study: Timber Frame Installation in Netley Grange, Southampton
- Commercial Decorating Services For Your Project’s Finishing Touch
- Choose An STA-Accredited Installer For Timberframe Installation
- Commercial Carpenters In Andover: How SC4 Can Help You Complete Your Project On Time
- Why The Right Second-Fix Construction Company Will Save You Time