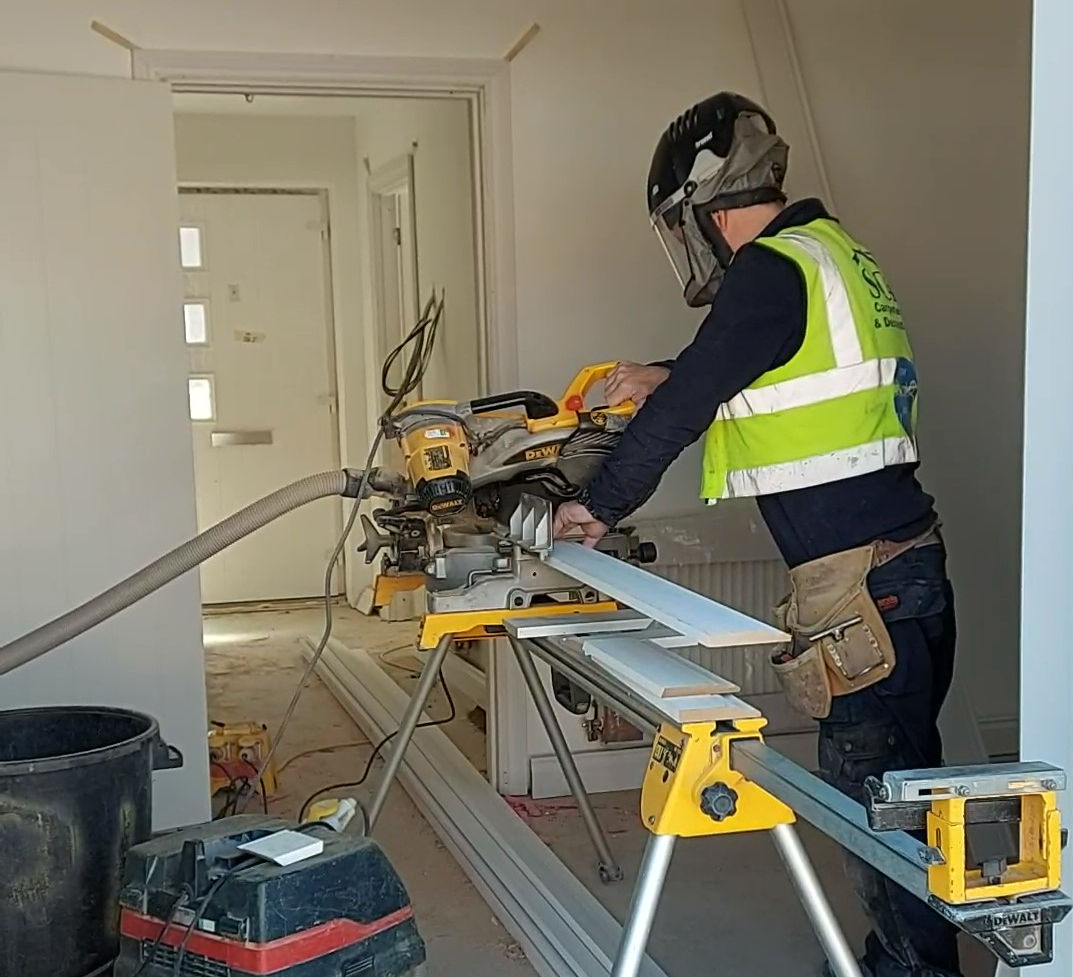
Carpentry Occupational Health Toolbox Talk
Carpentry presents a range of occupational health hazards that workers should be aware of. These include the inhalation of wood dust, injuries from manual handling, falls from elevated positions, and potential contact with hazardous chemicals and asbestos. Implementing robust safety protocols, notably the consistent use of personal protective equipment (PPE), is key to reducing these risks.
Here's a closer look at the primary risks and recommended safety measures:
Key Occupational Hazards in Carpentry:
- Wood Dust Exposure: Breathing in wood and MDF dust can lead to respiratory issues such as asthma. Certain hardwoods can also pose a cancer risk upon inhalation.
- Manual Handling Injuries: Lifting cumbersome materials and maintaining awkward body positions can cause back injuries and other musculoskeletal problems.
- Falls from Heights: Working on ladders, scaffolding, or other elevated platforms carries a significant risk of severe injuries from falls.
- Chemical Hazards: Contact with chemicals found in paints, adhesives, and wood preservatives can result in skin irritation and respiratory difficulties.
- Asbestos Exposure: Older building materials, including some wood, may contain asbestos. Inhaling asbestos fibres can lead to serious lung diseases.
- Noise-Induced Hearing Loss: The operation of power tools frequently exposes carpenters to high noise levels, which can cause permanent hearing damage.
- Eye Injuries: Airborne debris, wood splinters, and other particles can cause serious eye injuries if appropriate eye protection is not worn.
- Lacerations and Cuts: The use of sharp hand and power tools inherently carries a risk of cuts and lacerations.
- Slips, Trips, and Falls: Uneven work surfaces or cluttered work areas increase the likelihood of slips, trips, and falls.
Effective Safety Measures for Carpenters:
- Personal Protective Equipment (PPE) & Respiratory Protective Equipment (RPE): Consistent and correct use of PPE is vital. This includes wearing RPE (N95 or higher) to prevent wood dust inhalation, safety glasses or goggles for eye protection, and gloves to safeguard hands.
- Dust Prevention: Measures to protect against construction dust, including wood dust, should include:
- using local exhaust ventilation (LEV) – i.e. M-class extractors to minimise dust when using power tools,
- wearing appropriate respiratory protection (like dust masks), and
- following safe work practices.
- Proper Lifting Techniques: Learning and consistently applying correct lifting methods can significantly reduce the risk of back injuries.
- Safe Working Practices: Ensure all tools are well-maintained and in good working order. Maintain a tidy, organised workspace and minimise distractions to enhance focus and safety.
- Fall Protection Systems: When working at height using scaffolding, key requirements include fall protection measures (equipment such as harnesses, lanyards, and safety lines), proper scaffolding design, and regular inspections. Guardrails and toe boards are mandatory on scaffolding platforms 2 metres or higher. Employers must also ensure workers erecting, altering, and dismantling scaffolding are adequately trained. Additionally, scaffolding should be inspected before first use, after significant changes, and at least every seven days.
- Chemical Safety Protocols: Always read and understand the Safety Data Sheets (SDS) for any chemicals being used. Adhere strictly to the recommended precautions to prevent exposure.
- Asbestos Awareness and Precautions: Be vigilant about the potential presence of asbestos in older materials. If asbestos is suspected, appropriate safety protocols must be followed.
- Hearing Protection: Utilise hearing protection, such as earplugs or earmuffs, particularly when operating loud power tools.
- Eye Protection: Always wear safety glasses or goggles when engaged in activities that could generate flying debris or particles.
- Comprehensive Training: Ensure you receive thorough training on all relevant safety procedures, as well as the safe operation of tools and equipment.
Risk Assessments and Method Statements:
A Risk Assessment Method Statement (RAMS) is a crucial document that systematically identifies potential workplace hazards and details a safe, step-by-step approach to executing tasks. Essentially, it integrates a risk assessment with a method statement, serving as an indispensable tool in construction to promote workplace safety and ensure adherence to health and safety laws.
Core Elements of a RAMS:
- Risk Assessment: This component focuses on pinpointing potential dangers (such as working at heights or handling hazardous materials) and assessing the probability and severity of the risks associated with them.
- Method Statement: This section clearly defines a safe work procedure. It provides sequential instructions on how to perform a task safely, specifying necessary safety equipment and control measures to mitigate identified risks.
The Significance of RAMS:
- Improved Site Safety: RAMS play a vital role in identifying and managing potential risks, contributing to a safer working environment for everyone.
- Regulatory Compliance: These documents help businesses meet their legal obligations under health and safety regulations, including frameworks like the Management of Health and Safety at Work Regulations 1999.
- Clearer Communication: RAMS provide unambiguous instructions and set clear expectations for workers, thereby minimising the likelihood of errors and accidents.
- Enhanced Planning: They enable more effective preparation and coordination for various tasks and projects.
- Informed Safety Decisions: RAMS empower workers to make sound safety choices, particularly when addressing unexpected issues or changes.
Application of RAMS:
RAMS are widely utilised across numerous industries, especially those involving high-risk activities such as construction. Typically, they are formulated before work commences on a task or project, ensuring that safety considerations are integrated from the very beginning. Furthermore, RAMS are subject to periodic review and updates to maintain their relevance and effectiveness over time.
In summary, RAMS are far more than just procedural paperwork; they are practical instruments that actively contribute to creating a safer and more efficient workplace.
By understanding the risks and hazards and diligently implementing these safety measures, carpenters can significantly reduce their risk of occupational injuries and illnesses.
Download our Carpentry Occupational Health Toolbox Talk
Find Out More
To find out more, please take a look at our recent carpentry project portfolio, and feel free to get in touch if you would like to discuss your own requirements.
Click on the categories below to find out more about:
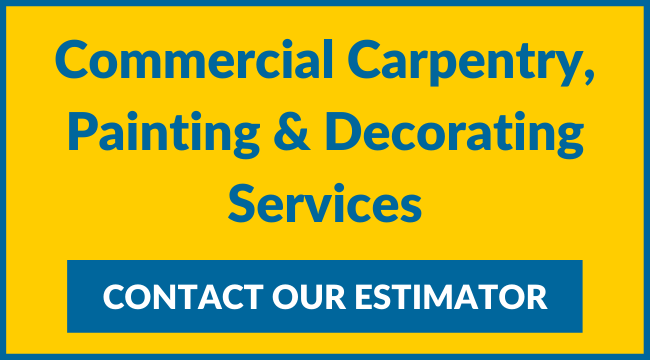
Connect with Us
Share this Page
More Posts
Recent Posts
- Our Favourite Carpentry Project Of 2024: Cromwell Court, Old Basing
- Case Study: Timber Frame Installation in Netley Grange, Southampton
- Commercial Decorating Services For Your Project’s Finishing Touch
- Choose An STA-Accredited Installer For Timberframe Installation
- Commercial Carpenters In Andover: How SC4 Can Help You Complete Your Project On Time
- Why The Right Second-Fix Construction Company Will Save You Time